The term grease is used to
describe a number of
semisolid
lubricants possessing a higher initial
viscosity than
oil. Although the word grease is also used to
describe
rendered fat of animals, in the context of
lubricants, it typically applies to a material
consisting of a
calcium,
sodium or
lithium
soap base
emulsified with
mineral or
vegetable oil.
A true grease consists of an oil and/or other
fluid lubricant that is mixed with another thickener
substance, a soap, to form a solid. The term soap
is used in the
chemical sense, meaning a
metallic
salt of a
fatty acid, which forms an
emulsion with the oil.[1]
Greases are a type of shear-thinning or
pseudo-plastic
fluid, which means that the viscosity of the fluid
is reduced under
shear. After sufficient force to shear the grease
has been applied, the
viscosity drops and approaches that of the base
lubricant, such as the mineral oil. This sudden drop in
shear force means that grease is considered a
plastic fluid, and the reduction of shear force with
time makes it
thixotropic. It is often applied using a
grease gun, which applies the grease to the part
being lubricated under pressure, forcing the solid
grease into the spaces in the part.
Soaps are the most common emulsifying agent used, and
the type of soap depends on the conditions in which the
grease is to be used. Different soaps provide differing
levels of temperature resistance (relating to both
viscosity and volatility), water resistance, and
chemical reactivity. Powdered solids may also be used,
such as
clay, which was used to emulsify early greases and
is still used in some inexpensive, low performance
greases.
The amount of grease in a sample can be determined in
a
laboratory by extraction with a
solvent followed by e.g. gravimetric determination.
Greases are used where a mechanism can only be
lubricated infrequently and where a lubricating oil
would not stay in position. They also act as valuable
sealants to prevent ingress of water and dust.
Grease-lubricated bearings have greater
frictional characteristics due to their high
viscosity. Under shear, the viscosity drops to give the
effect of an oil-lubricated bearing of approximately the
same viscosity as the base oil used in the grease.
Lithium-based greases are the most commonly used; sodium
and lithium based greases have higher melting point
(dropping point) than calcium-based greases but are not
resistant to the action of
water.
Lithium-based grease has a dropping point at 190 °C
to 220 °C (350 °F to 400 °F). However the maximum usable
temperature for Lithium-based grease is 120 °C.
Grease used for axles are composed of a compound of
fatty oils to which
tar,
graphite, or
mica is added to increase the durability of the
grease and give it a better surface.
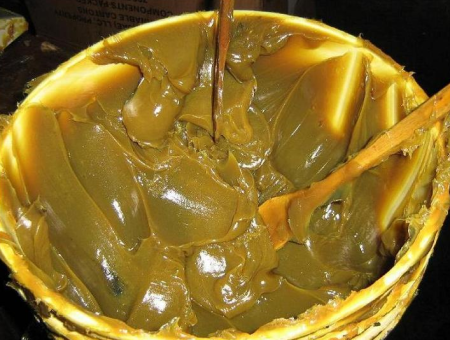
Teflon is added to some greases to improve their
lubricating properties. Gear greases consist of
rosin oil, thickened with
lime and mixed with mineral oil, with some
percentage of water. Special-purpose greases contain
glycerol and
sorbitan esters. They are used, for example, in
low-temperature conditions. Some greases are labeled
"EP", which indicates "extreme pressure". Under high
pressure or shock loading, normal grease can be
compressed to the extent that the greased parts come
into physical contact, causing friction and wear. EP
grease contains solid lubricants, usually graphite
and/or
molybdenum disulfide, to provide protection under
heavy loadings. The solid lubricants bond to the surface
of the metal, and prevent metal-to-metal contact and the
resulting friction and wear when the lubricant film gets
too thin.